Call us: +1 315 791 4196 | Email: info@trayotek.com
SLA Stereolithography
Stereolithography Apparatus (SLA) is a 3D printing technique that transforms UV-sensitive liquid photopolymer resin into solid objects, layer by layer. This process, called photopolymerization, involves selectively solidifying the liquid resin using a UV laser beam.
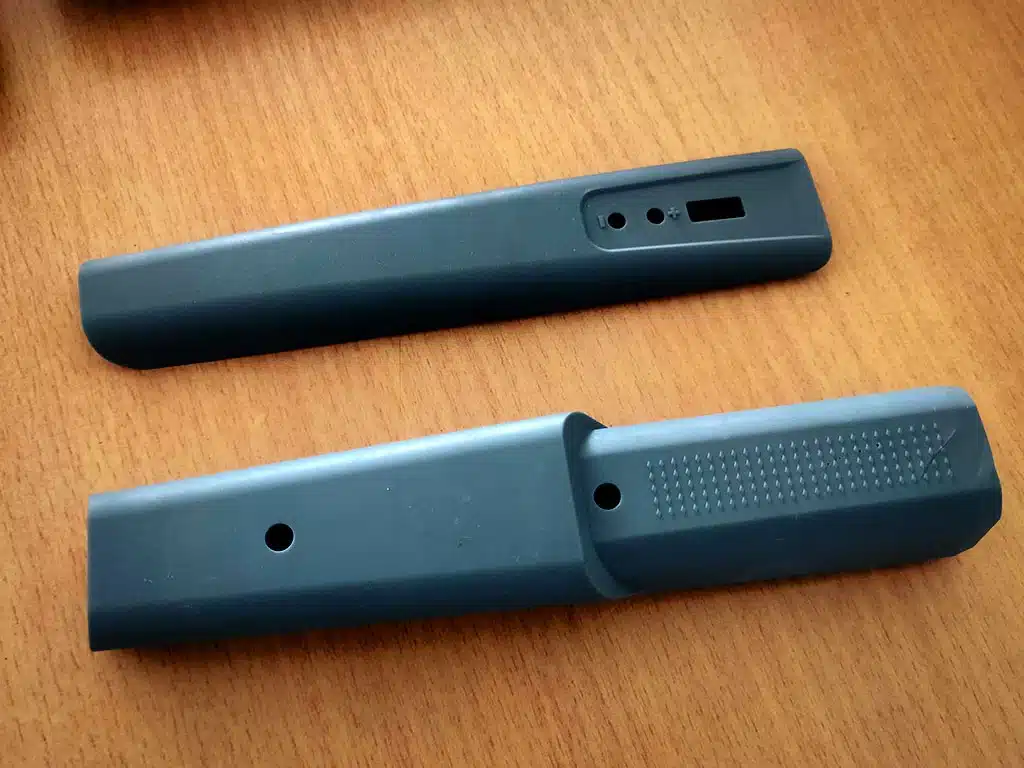

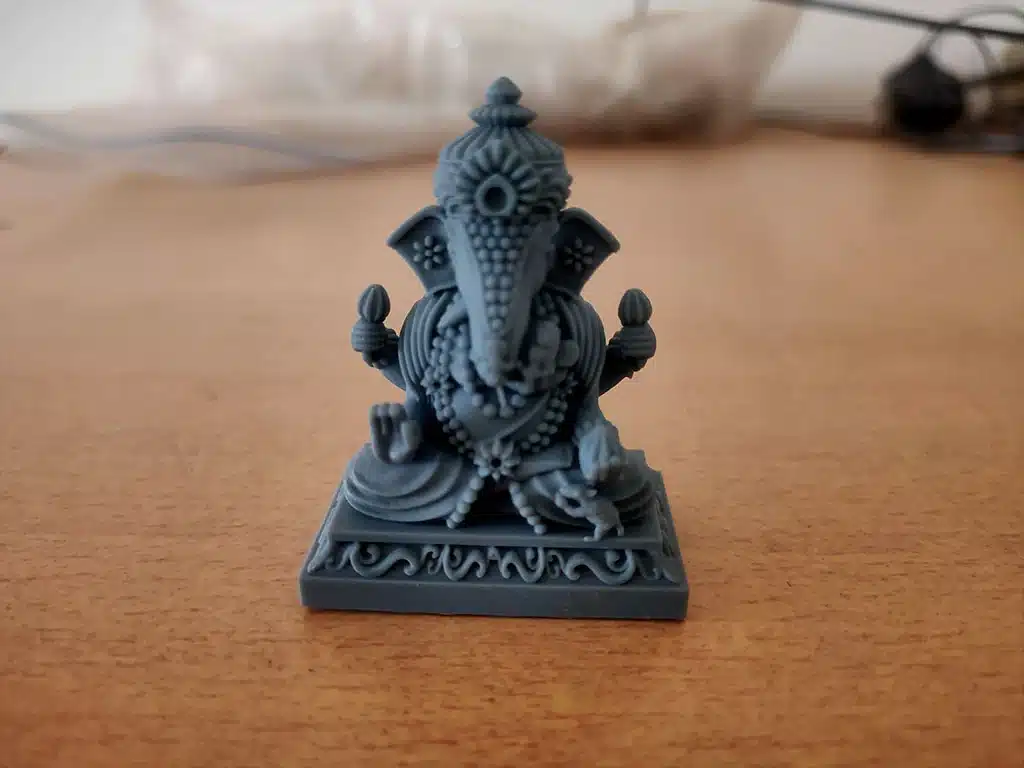
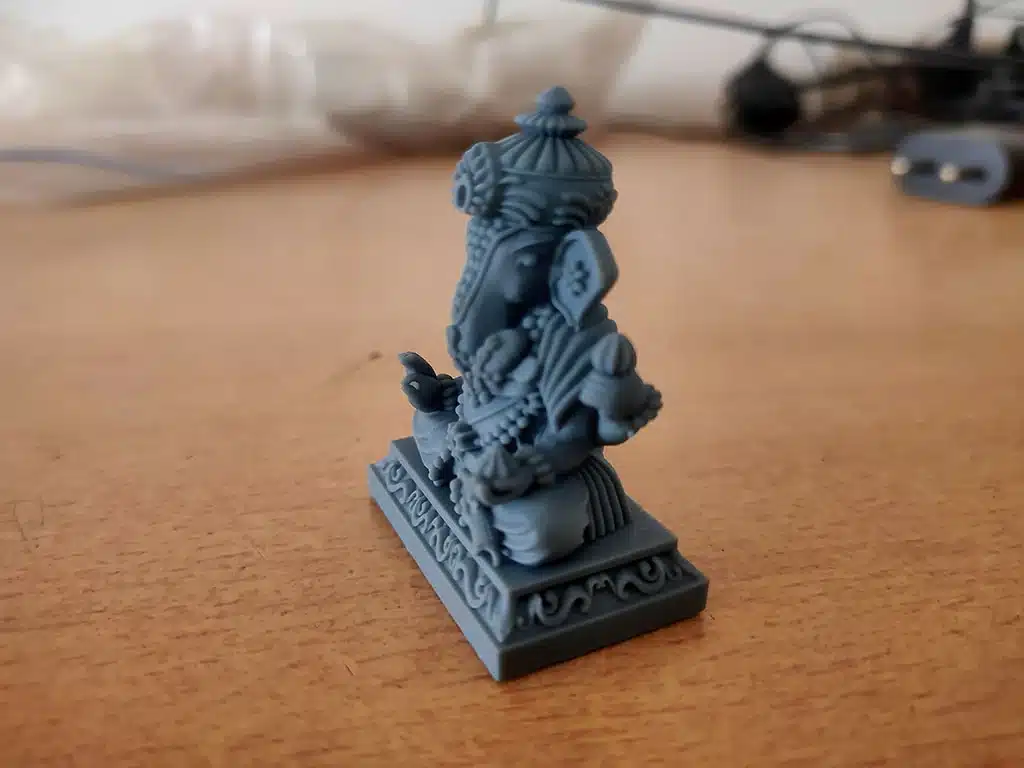

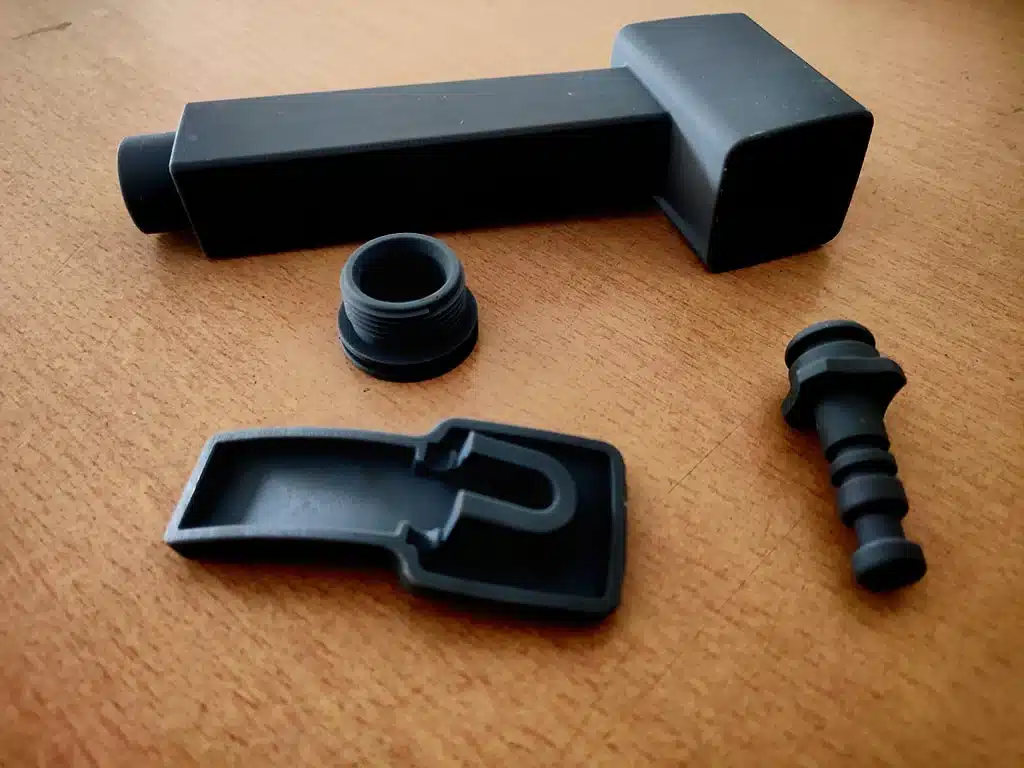
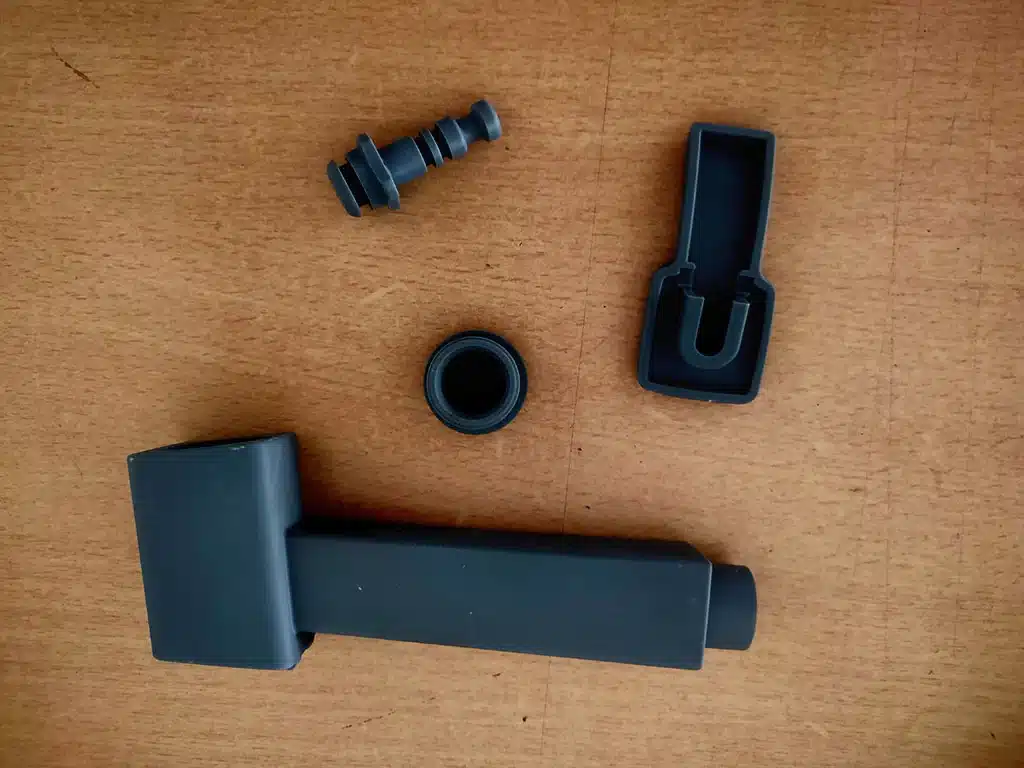
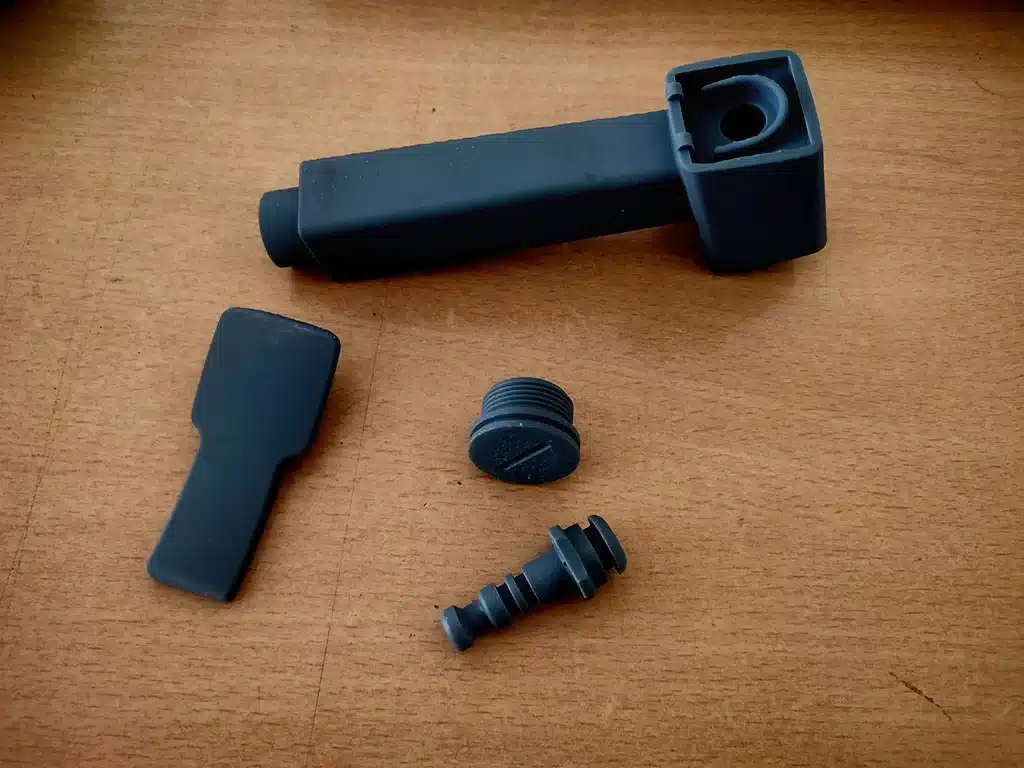
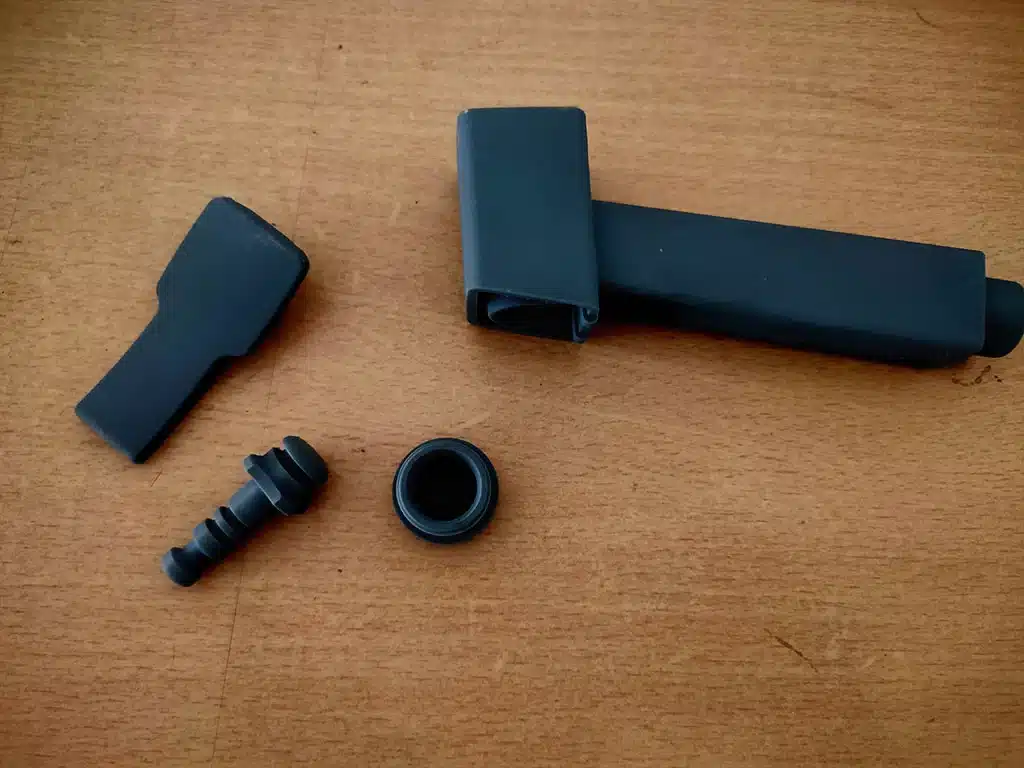
SLA (Stereolithography Apparatus) 3D Printing Services
In stereolithography, the manufacturing area is located directly above the liquid resin tubes, which are spread with resin. The ultraviolet laser then selects grass and cures the resin in a predetermined manner. A UV laser then selectively cures the resin along a predetermined path, solidifying it. After completing each layer, the platform lowers into the tank, allowing a new layer of resin to be applied. This process repeats until the entire part is formed.
The liquid resin consists of chemicals that react to UV light, causing them to bind and solidify. This reaction is permanent, and SLA parts cannot revert to their liquid state; when heated, they burn instead of melting. This behavior is due to the use of thermoset polymers in SLA, unlike the thermoplastics used in FDM printing.
SLA technology excels at producing accurate and precise parts quickly, and has the smoothest surface of all 3D printing techniques. However, SLA components are generally fragile and can deteriorate over time when exposed to sunlight, making them unsuitable for functional models.
SLA 3D Printing Applications
- Master copies for vacuum casting and other low-volume prototyping techniques
- Patterns for investment casting
- Low volume/ limited edition products especially for complex geometries
- Dental/ jewelry/ art and other sectors which require high detailing and finish
- Visual prototypes for photo shoots and market testing
- Parts with high dimensional accuracy with intricate details
- Low-volume production of complex geometries
- Parts for testing form, fit, and assembly
Suitable Materials for SLA
- Clear resin
- ABS-like White Resin
- Grey Resin
- Flexible Resin
- Castable wax Resin
Technical requirements For SLA
- Standard Lead time: Minimum 4-5 working days depending on part size, number of components, and finishing requirements lead time may increase.
- Standard Accuracy: ± 0.025mm – 0.05mm
- Layer thickness (resolution): 0.016 mm
- Minimum Wall thickness: 1mm
- Max dimensions: 330mm x 185mm x 400 mm. Large parts can be created by assembling individual parts by interlocking designs or gluing them together.
- Surface finishing and Post Processing: Unfinished SLA parts usually display visible building layers on their surfaces. However, various post-production finishing techniques can be applied to achieve a range of effects, from high gloss finishes to coarse textures. These parts can undergo processes such as sandblasting, smoothing, coloring or impregnating, painting, varnishing, covering, and coating to enhance their appearance and functionality.